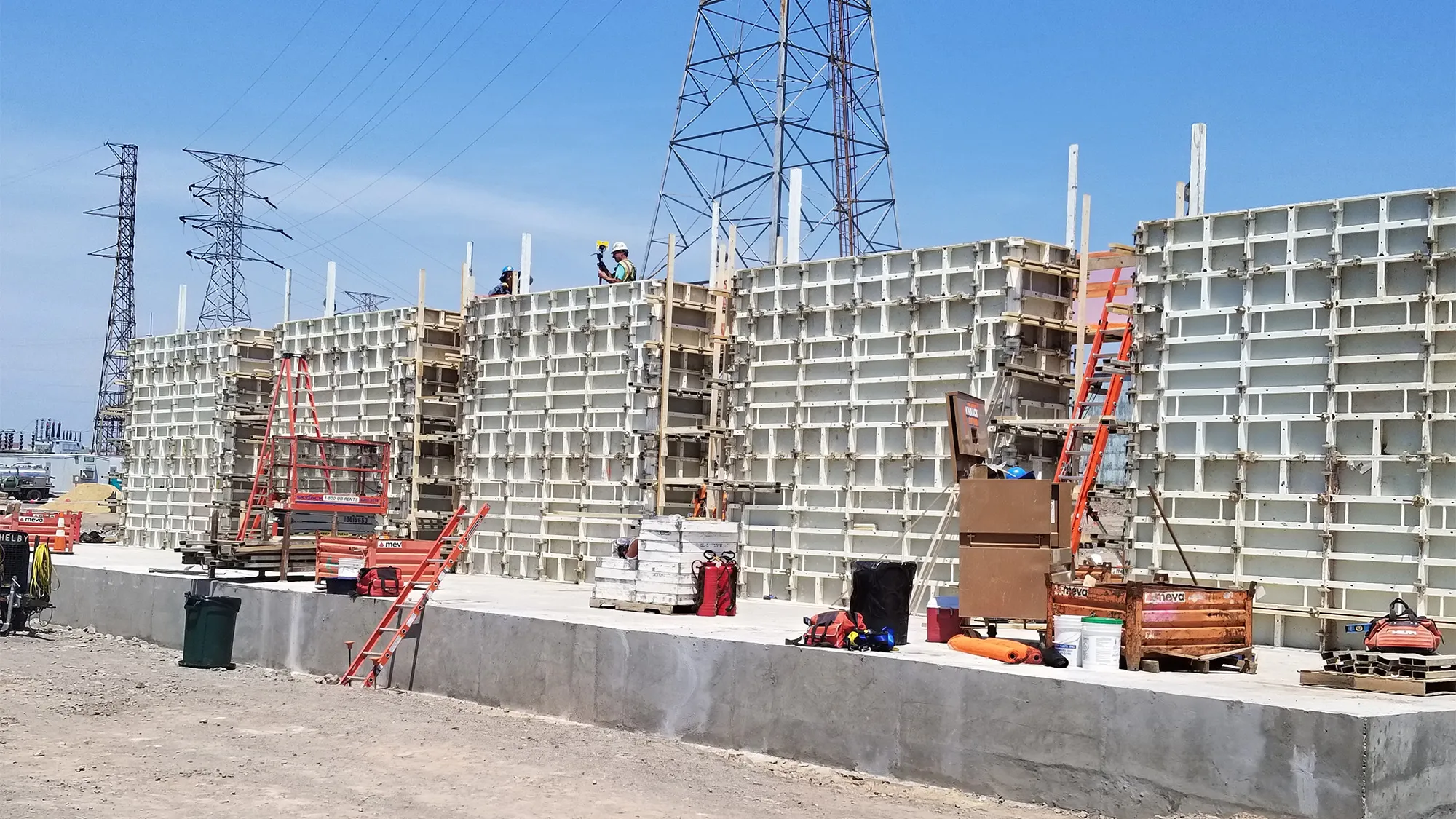
Air Separation Unit Project
Project Overview
Riggs Distler was contracted to provide heavy civil, mechanical piping, and equipment setting services to support the construction of an Air Separation Unit in Pennsylvania. The Air Separation Unit serves many important industrial and commercial purposes, and will ultimately produce oxygen, nitrogen, and argon for medical applications and hospital settings, chilling and freezing food products, metal fabrication, blanketing and purging, and combustion enhancement.
This complex project requires close coordination between our Heavy Civil and Mechanical groups. Riggs Distler’s unique ability to share knowledge across disciplines and provide turnkey construction services under one hat allows us to carefully orchestrate every stage of the project schedule, realize efficiencies and cost savings for the client, and deliver the project on budget and schedule.
Challenges Overcome
Since the client plans to build multiple air separation units throughout the United States, the original project plans were engineered using a “one-size-fits-all” approach. As a result, site-specific considerations were not taken into account, resulting in a number of design conflicts. To address these issues, Riggs Distler’s Heavy Civil group put their extensive knowledge to work, collaborating with the Mechanical group, surveyors, and project owners to develop smart and expedient design solutions without significant delay.
Throughout the project, Riggs Distler worked closely with the client and project engineers to adapt the plans to the jobs at hand, resolve conflicts, and execute the work to the highest standard. To better serve the client and account for our adjustments to the project plans, Riggs Distler transitioned the Mechanical work scope to a Time and Materials contract, resulting in significant cost savings for the client. During the planning stage, our team was also able to identify a number of permitting issues that could have resulted in significant delays. By carefully reviewing construction packages, Riggs Distler was able to notify the site team of these issues and deal with them in advance, before they became problems.
Riggs Distler’s team also encountered challenges in organizing and procuring the right materials for the job. All valves, instruments, and specialty items were provided by the client, and due to organizational issues, they were not easily identifiable. The project needs to be completed under an aggressive schedule to meet the demands of the Northeast region’s high-volume market, and better organization was needed to ensure efficient execution. Riggs Distler performed a comprehensive inventory of all project materials and organized them in a specialized warehouse, greatly improving our ability to secure the right components and improving efficiency during all stages of the project.
Services
Industrial Generation
Mechanical
Heavy Civil
Our work included:
Heavy Civil:
- Preparing and building equipment foundations (involved pouring more than 4,000 cubic yards of concrete)
- Sewer systems.
- Electrical ductbank work.
- Installing chilled water supply and return piping.
- Industrial waste and water service piping.
Mechanical Scope:
- Receiving and handling equipment supplied by our client.
- Installing all necessary equipment, such as cold boxes, compressors, pumps, piping skids, vessels, truck scales, modin, a scale house, a transformer, and PDC (power distribution center).
- Grouting and anchoring equipment.
- Supplying and installing interconnecting piping, inline instruments, ship-loose items, and supports.
- Installation of structural steel as called for in drawings provided.
- Supplying and installing insulation per engineering drawings (excluding perlite).
- Preserving equipment during construction and commissioning.
Riggs Distler is also responsible for all procurement, fabrication, installation, cleaning, testing, and pipe painting.
Results Delivered
Riggs Distler takes great pride in our ability to assist clients that provide essential public services. Our ability to perform complex work as one unit across multiple disciplines enabled us to greatly improve efficiency, reduce costs, and meet a fast-paced schedule for this important project.